Silicone co-extrusion process
What is Co-Extrusion?
At Merefsa, we specialize in the production and supply of custom silicone extrusion profiles. This process can be extended to co-extrusion, an advanced technique that combines two or more materials to obtain products with enhanced properties.
Among the options we offer are:
- Use of two types of silicone: solid HTV and sponge HTV.
- Different silicone formulations, adapted in hardness and color according to customer specifications.
- Silicone combined with other materials, including metal or textile inserts, which reinforce and enhance the characteristics of the final product.
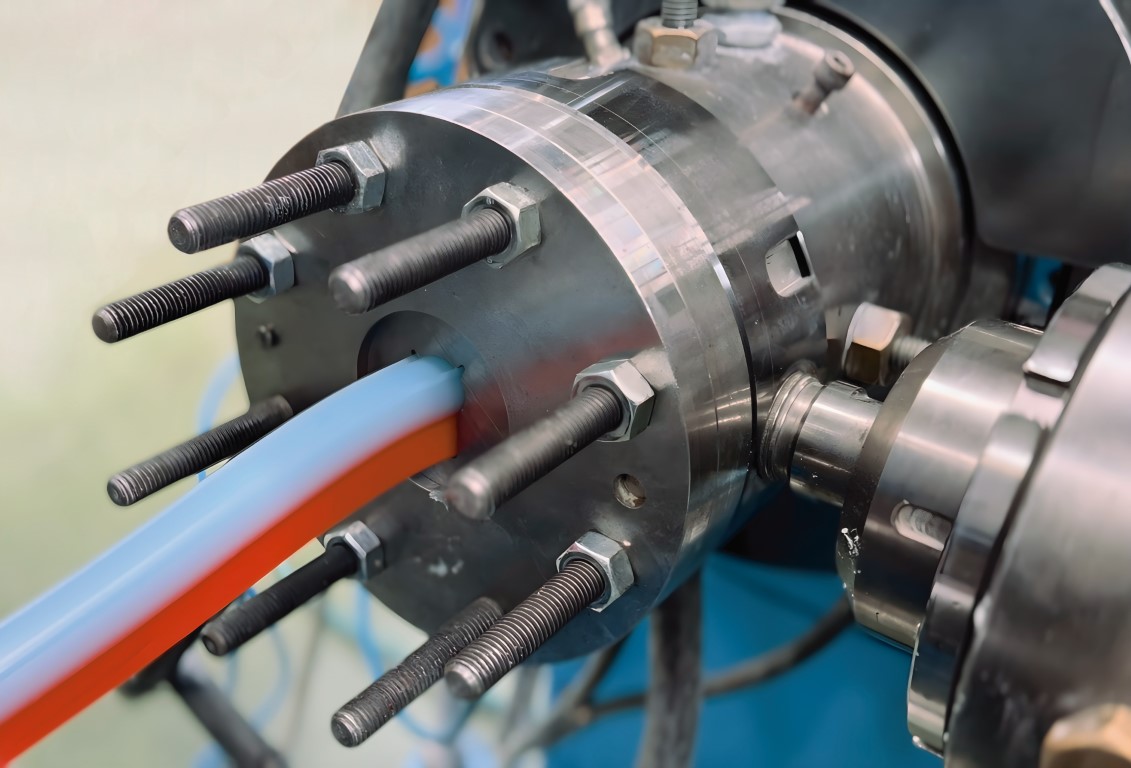
Characteristics
Merefsa's Technical Office and Machining departments are responsible for the design and production of silicone co-extrusion profiles, based on a physical sample or drawing provided by the customer.
Our solutions include:
- Hardness ranging from 20 to 85 Shore A in compact HTV silicone.
- Availability of any basic and RAL color.
- Special formulations with high mechanical resistance.
- Operating temperature range from -90ºC to +315ºC.
- Compliance with FDA and BfR non-toxicity standards.
- EN 45545 certification for railway transport applications.
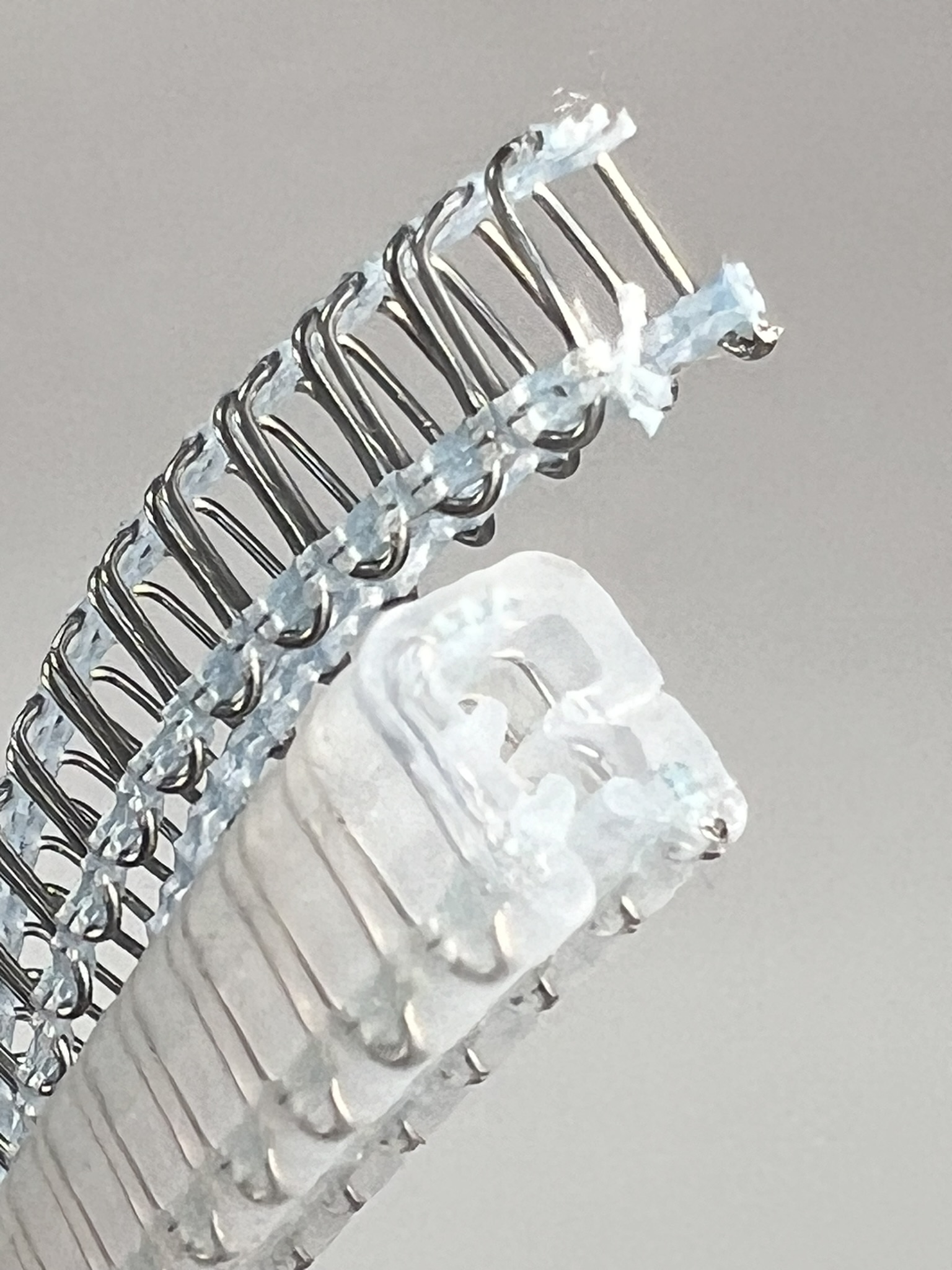
Applications
Silicone co-extrusion profiles are used in a wide range of applications across various industries, thanks to their exceptional high-temperature resistance, durability, UV resistance, and non-stick and dielectric properties.
Some of the main applications include:
- High-quality, energy-efficient LED lighting profiles.
- Seals and gaskets for the food industry, especially for food processing and packaging.
- Profiles for the medical industry, used in diagnostic devices and equipment.
- High-temperature sealing profiles for ovens and engines.
- Insulation profiles against heat, sound, and vibration transfer, used in sectors such as construction, home appliances, railway transport, and more.
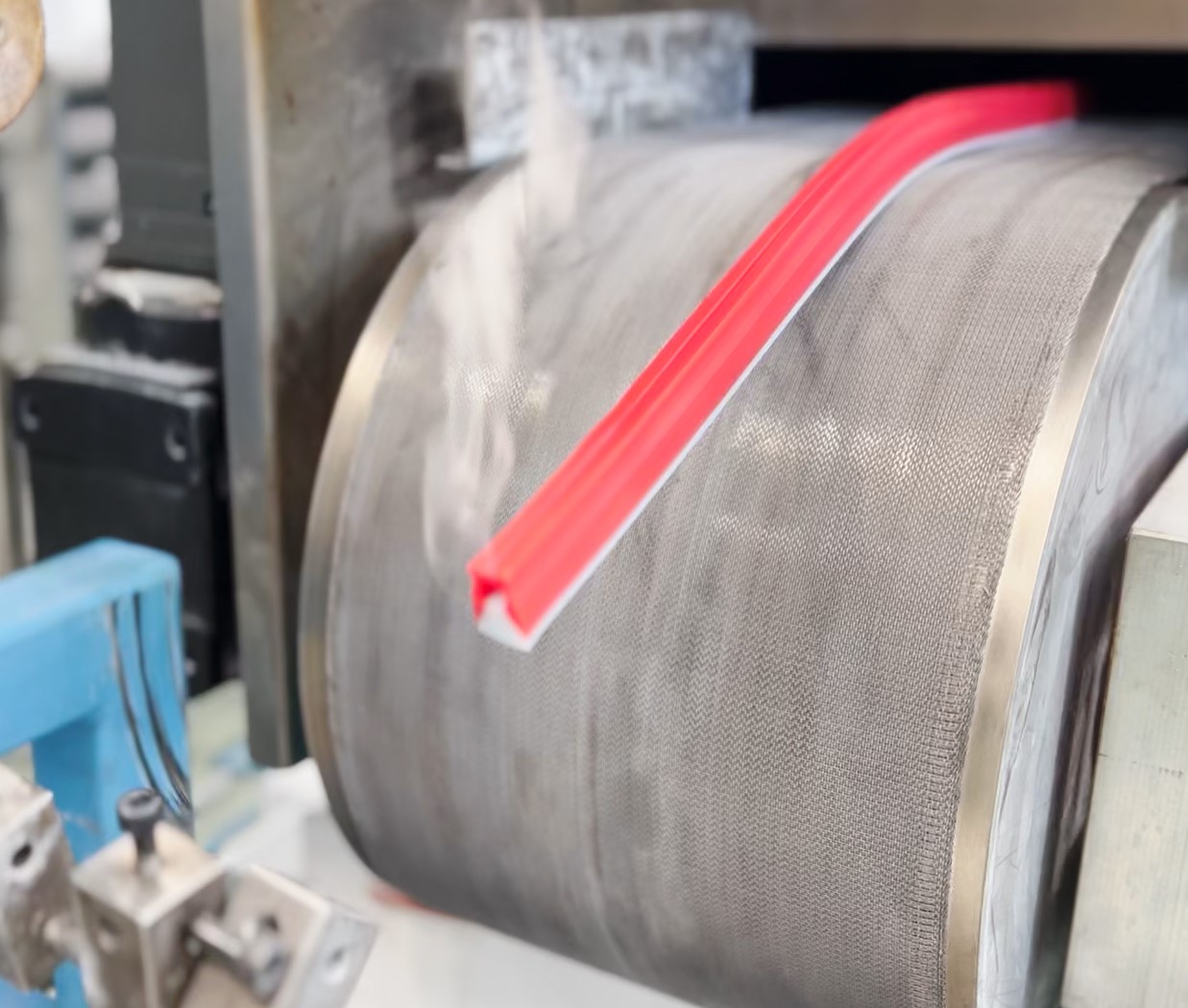